Metal Roof Retrofit Means Energy, Cost Savings
Goodfellow Air Force Base, San Angelo, TX
View Case Studies
It may seem counterintuitive, but in today’s world of renewable energy and sustainability, retrofitting means forward-thinking. A key leader in new building technologies and energy efficiency is outside the private sector and is, in fact, the federal government, including the Department of Defense (DOD). Being the military, motivations are clearly defined: The DOD is required under law to produce or procure 25% of all energy from renewable sources by 2025 and is mandated to reduce energy use on its properties by 30% by 2015 and
by another 37.5% by 2020.
The military also provides grants to companies that provide novel technologies, products, and systems to help the DOD meet its energy and water conservation goals. In 2010, a team of leading metal construction companies and MCA, Glenview, IL, were awarded a $1 million Environmental Security Technologies Certification Program (ESTCP) grant to develop a retrofit metal roof system with integrated renewable energy technologies,
including an integrated assembly of six different roofing system components.
Goodfellow Air Force Base (AFB) Project
The project involved retrofitting an 11,900-ft metal roof on a 10,000-ft “security forces” building at the Goodfellow AFB in San Angelo, TX. According to Scott Kriner, MCA’s technical director, the project was unique
because “it is the only retrofit metal roofing system integrating other energy-saving technologies to form a building envelope.”
Prior to the installation, the Department of Energy’s Oak Ridge National Laboratory (ORNL) installed a data acquisition system to monitor the building’s temperature and heat information. Both energy data and utility billing information were collected. After a baseline energy usage was established, installation of the retrofit metal roof system began in April 2012. Two months later, it was completed.
The project’s main achievements include
- integrating roofing system components into one retrofit system that will maximize electricity generation and minimize the cooling load of the building. “The solar-thermal technology that is integrated into the retrofit cavity will optimize the energy generated for domestic hot water and for space heating,” Kriner said. This solar-thermal technology is expected to yield more than 750,000 KBTU of energy per year. With local utility costs taken into account, the AFB is projecting a savings in energy costs of $11,750 per year.
- capturing rainwater on the metal roof in an aboveground cistern with a 10,000-gallon capacity. The roof is expected to capture about 131,000 gallons of potable water, which will be used for irrigation purposes on the AFB. Future plans call for the ORNL to continue monitoring data on temperatures, heat transfer, energy output from the PV, energy consumed by the building, and water usage for the next year. Kriner is hopeful about the results. “The ESTCP, DOD, and the project team are confident that this integrated retrofit roof system will perform as predicted and allow for the technology to be transferred throughout the DOD, to other federal agencies, and into the commercial building sector,” he said.
How Integrated Technologies Were Installed
- Structural purlins were installed over the existing metal roof.
- Additional insulation, using rigid insulation board, was placed over the existing roof to meet the current code requirements.
- A waterproof roof underlayment was then applied over the insulation.
- A radiant barrier was installed over the underlayment.
- An integrated solar-thermal system, using a closed-loop tubing array with a waterglycol mix heat-exchange medium, was installed over the radiant barrier to optimize heat transfer.
- The thermal purlin used to position the solar thermal system tubing was configured to allow for above-sheathing ventilation (convective cooling) to take place from the eave to the ridge.
- Panels of 24-gauge standing-seam metal roofing, which had been prepainted with a polyvinylidene fluoride cool coating, were laminated with a thin-film PV system and then installed directly over the solar-thermal system.
Metal Industry Leaders Involved in the Project
- David Dodge, president, and Jeff Slagle, project manager, Paramount Metal Systems, Little Rock, AR
- Tom Evans, national business development manager, Dow Building Solutions, Midland, MI
- Scott Kriner, technical director, Metal Construction Association, Glenview, IL
- Dale Nelson, president, and Mark James, vice president, Roof Hugger, Odessa, FL
- William Poleatewich, director of new technologies, Pfister Energy, Hawthorne, NJ
- Robert Scichili, president, Robert Scichili Associates, Richardson, TX
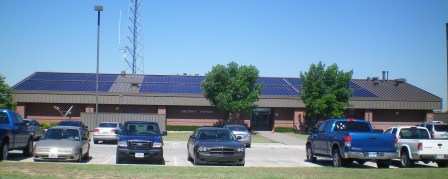
Click to enlarge photos